Hydraulic dump pumps are integral to the efficient operation of dump trucks, providing the power necessary to lift and lower heavy loads with precision and reliability. Understanding these essential components is crucial not only for operators but also for maintenance professionals and anyone involved in heavy equipment management. This article aims to demystify the inner workings of hydraulic pumps for dump trucks, offering a detailed exploration of their core components, functionality, and importance. By the time you finish reading, you’ll have a clearer understanding of how hydraulic systems optimize performance, ensure safety, and contribute to the overall productivity of dump trucks in demanding applications.
Types of Hydraulic Pumps for Dump Trucks
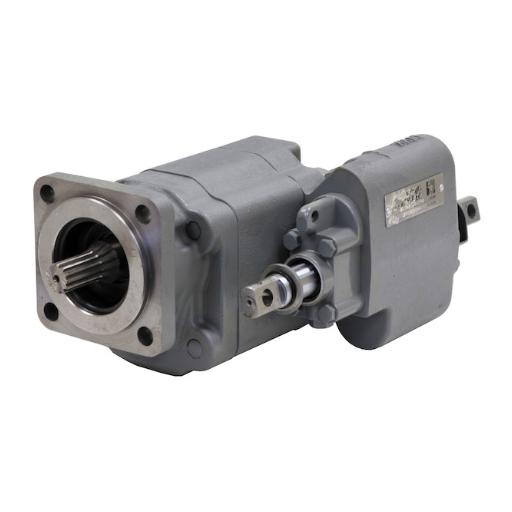
Gear Pumps
Gear pumps are one of the most common types of hydraulic pumps utilized in dump trucks due to their simplicity, reliability, and cost-effectiveness. The operation generates pressure with the meshing of gears to force hydraulic fluid through the system. Such a design is, in fact, very suitable for dump truck operations since they have heavy-duty functions, with hydraulic power being delivered constantly to lift and lower heavy loads.
The pump traps fluid between the teeth of two meshing gears inside a casing that is tightly sealed. As the gears turn, fluid is sucked into the cavity of the pump, pressurized in transit through the gear assembly, and then released to the hydraulic system. The operation of the gear pump is steady in the process, ensuring reliability in high-pressure situations such as lifting the dump bed.
Even though they are powerful and very easy to manage, these pumps do have some drawbacks. Gear pumps generally produce less efficiency compared to more advanced types of hydraulic pumps, such as piston pumps, and they may produce increased noise levels due to their mechanical operation. The durability and simple maintenance, however, still make them good candidates for mainstream use in heavy-duty applications.
Piston Pumps
Piston pumps are hydraulic pumps known for their versatility and efficiency in handling applications where a very high-pressure performance is required high performance and demand are placed on a task in any industry. In operation, these pumps use one or more reciprocating pistons to move the hydraulic fluid, thereby providing a precise and accurate output. The construction of piston pumps enables them to operate under higher pressure and flow than simpler pump types like gear pumps; thus, they are more apt for applications demanding the highest performance and efficiency.
A huge benefit of piston pumps is that their operation stays efficient under high-pressure conditions. These pumps operate at pressures over 6,000 psi and find application for heavy machinery, construction equipment, and industrial systems. Another feature that keeps these hydraulics running for long periods without giving in is the minimization of leakage and energy waste over time due to modern designs. And with these latest designs, hydraulic operators can now ensure variable displacement for maximum versatility tailored to individual operational needs.
However, piston pumps are also more complex to manufacture and maintain, thereby rendering a relatively high price compared to gear or vane pumps. Due to the intricacy of their design, they require very high tolerances in machining and much care when being serviced. They usually pay for themselves by being so highly compound efficient, with a long life under working conditions that can almost be considered harsh, especially in those systems where operational efficiency and reliability are of paramount importance. These qualities have thus cemented the position of piston pumps in the best hydraulic applications today.
Vane Pumps
Vane pumps are a kind of displacement pump that has seen widespread use in hydraulic systems. The reason: small in size and a bit more reliable than other types of pumps in low and medium pressures. It consists of a rotor having extendable vanes that slide against the cam ring, forming chambers of variable volume to draw and discharge fluid. The design of the pump delivers a smooth flow with very little pulsation; hence, it is suitable for systems that require steady operation.
Vane pumps are very efficient for handling fluids of low to medium viscosity. This makes them very versatile for applications in automotive transmissions, industrial machinery, and mobile hydraulic systems. They also run relatively quietly when compared to other types of pumps, and this becomes important in environments sensitive to noise. Their straightforward working mechanism also makes them easy to maintain and thereby ensure a longer working life, provided that the vane pump runs under adequate operating conditions.
However, there are limitations. They tolerate contamination less, and hence, performance can deteriorate with abrasive and corrosive fluids. Thus, one needs to ensure proper filtration and periodic maintenance to get the best out of a vane pump. Still, under suitable conditions, vane pumps form a strong, cost-effective choice in hydraulic systems, emphasizing efficiency, compactness, and noise levels.
Applications of Hydraulic Dump Pumps

Construction Industry
Hydraulic dump pumps, due to their reliability and ability to undertake heavy-duty processes, find a myriad of applications in the construction industry. Being the lifeblood of hydraulic systems attached to dump trucks, excavators, loaders, and any machinery requiring direct hydraulic manipulation, their technical design caters to quietly lifting and lowering heavy objects with minimal energy loss, thus contributing to the productivity of operations on-site.
Hydraulic dump pumps present a variable rate and pressure adaptation fitting for the scope of construction activities. Modern dump pumps are designed to handle hydraulic fluid pressures well above 3,000 PSI to lift the heaviest loads, even in exceedingly demanding operations. Their small, durable construction also reduces downtime, thereby enhancing the durability of the equipment as a whole.
Hydraulic dump pumps further make dumping of material, such as gravel, sand, or debris, easy, thereby increasing site safety and efficiency, decreasing drilling time, and lessening manual labor intensity. Paired with hydraulic technology advancements, like smart control systems, they present better monitoring and regulating of force, pressure, and speed. These traits are highly favored within the construction world for gaining precision, efficiency, and sustainability in operations.
Mining Operations
Technology in mining has greatly evolved, bringing in efficiency, environmental considerations, and worker safety. Autonomous mining equipment is certainly one such innovation. The tasks of excavation, hauling, and material handling with intermittent human intervention are practiced using sensors, GPS technology, and machine-learning algorithms. The autonomous systems reduce downtime and, more importantly, mitigate accidents in hazardous working environments.
Moreover, the mine data-based approach processes assets using methods such as real-time monitoring and predictive maintenance. Sensor-based systems provide constant feedback regarding the condition of an asset so that operators can prevent a failure before it happens, thereby increasing uptime and extending asset life. On the other hand, improvements in ore-processing technologies-high-pressure grinding rolls (HPGR) and energy-efficient flotation methods-have allowed greater recovery while reducing costs, energy, and further carbon footprints.
The evolving tools indicate the resort to sustainable and technology-driven mining techniques that are scalable within set, stringent environmental laws.
Waste Management
Proper waste management during mining is critical for reducing environmental hazards and satisfying the regulatory requirements. Since the downtimes of tailings storage facilities pose risks of leakage and failure, advanced waste management is being considered. Recently, dry stacking has become more and more popular because of the increased safety measures it provides when compared to wet storage, which simply involves drying the tailings so that they become a more stable waste form.
Moreover, further processing for secondary utilization of wastes is increasingly being worked on in many mining operations, with some recycling measures being adapted along the way. For example, trying to recover some residual values in older tailings may serve to reduce the volumes of waste and increase the efficiency of the use of resources. The use of geotechnical monitoring systems together with predictive analytics platforms has allowed waste facility operators to recognize potential issues in waste management on the fly, allowing mitigation and adjustments in operational workflows.
With waste management interfacing with advanced monitoring technologies and sustainable processes, the mining industry is stepping up its ecological accountabilities while realizing its operational efficiency.
Benefits of Using Hydraulic Dump Pumps
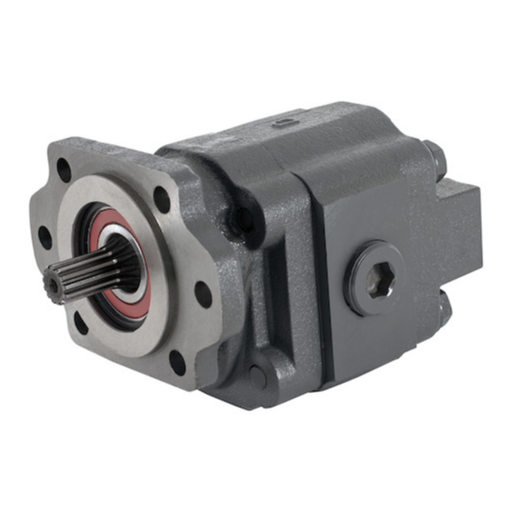
Increased Efficiency
As hydraulic dump pumps have been employed in many industries, including construction, mining, and waste handling, their advent has considerably transformed efficient operations. They enhance control over hydraulic systems rapidly and accurately during the lifting, lowering, and tilting of heavy loads. With many hydraulic systems, operators are going through mechanical or manual means in handling repetitive tasks for a longer time to achieve more work in a shorter period. Better workflow cuts down on downtime and allows for meeting schedules that demand high output without compromising safety or operational standards.
Modern hydraulic dump pumps are now supported by automation and adaptive mechanisms, utilizing intelligent technologies to optimize performance under various load conditions. Sensors and programmable logic controllers are integrated into these systems to dynamically adjust pressure and flow for specific task demands. The overall positive impact energy efficiency uses grid force only when needed, thereby reducing fuel consumption, operational costs, and environmental load. This precision aids in cost savings and increases the lifespan of the equipment by preventing over-exertion that leads to excessive wear.
Hydraulic dump pumps also encourage environmentally friendly activities. Reduced emissions from construction and industrial machinery are another ideal opportunity created by the reduction of fuel power usage. New advances, including the development of IoT-enabled monitoring systems, assist operators in collecting real-time data, analyzing system performance, and proactively addressing inefficiencies. Using this data-driven approach will guarantee that hydraulic systems are always functioning at optimum efficiency, thus providing a more sustainable, cost-effective, and reliable mode of operation for both small- and large-scale projects.
Enhanced Load Handling
The enhanced load-handling capability is the modern hydraulic system aspect intended for dealing with higher operational loads so that the system remains within proper limits. Through enhanced load sensing, hydraulic systems can apply dynamic adjustment of pressure and flow with respect to load requirements on demand. This saves energy, reduces wear and tear of the system components, and increases their operational life. Electronically controlled variable displacement pumps further fine-tune the operation for better performance under varying load conditions.
Material advances and engineering improvements have also benefited the load handling capabilities. High-strength alloys and composite materials used in hydraulic components provide better durability and resistance to extreme working conditions. As an example, advances in seal technology have greatly reduced the risk of leakages while maintaining performance and lessening downtime for maintenance. These materials do well in high pressures, thus being apt for applications such as construction, mining, and aerospace industries.
Further, employing an array of IoT-enabled sensors drastically changes traditional monitoring and management techniques of load handling. Such sensors gather and send real-time, insightful data on pressure, temperature, and viscosity to operators, allowing them to anticipate trouble and make correct judgments. Complemented by a cloud-based analytics platform, the data predicts load variations, prescribes inefficiencies, and schedules preventive maintenance preceding actual occurrence. Not only does this setup guarantee increased reliability, but it also ensures conformance to safety regulations, eventually producing sturdier adaptive hydraulic systems.
Improved Safety Features
Modern hydraulic systems have several state-of-the-art safety measures in place to eliminate risks before the system can harm people. Fail-safe devices such as pressure relief valves and load-holding valves are perhaps the most critical, preventing such issues as overloading of the system and unintended movements of actuators. These safety devices allow for enhanced safe operation for the operators and save the hydraulic components from destruction, which can occur when excessive load or mechanical wear act upon them.
These advanced measures in monitoring safety behavior use sensors and real-time data acquisition to identify behaviors that might be considered unusual at an early stage. First, the system continuously monitors such critical factors as fluctuation of pressure, oil temperature, and fluid contamination. The data are then analyzed through complex algorithms located in a secure cloud-residing platform. This model of prediction gives insight into potential hazards that operators can address well before they erupt into a probability of endangerment, thus allowing any necessary remediation to be carried out preemptively.
Ergonomics coupled with hydraulic principles has helped create an interface and a control system that is straightforward and less prone to human error. The systems are readily usable and equipped with automatic shut-off triggered by emergency signals, which, in cases of real danger, extinguish almost all manual interventions. The fusion of reliable and state-of-the-art hardware and the intelligent software system has put modern hydraulic applications not only above the safety threshold but also bestowed upon the field the highest level of operational safety across an array of applications.
Maintenance Tips for Hydraulic Dump Pumps
Regular Inspection Procedures
Regular inspection of hydraulic dump pumps is crucial to ensure they will always perform optimally and extend the operational life of the equipment. First of all, I suggest visually checking the whole outside of the dump pump, which includes the hose, fitting, and seals. Any observed sign of wear, cracking, or leaks must be remedied immediately, as arresting these may render the dump pumps in full operation. Next, check the level of hydraulic fluid with the reservoir gauge. Having a low fluid level may cause cavitation, overheating, or damage to internal components of the pumps.
Inspect next the status of the hydraulic fluid, as its health is vital to the performance of the system, and compromises will accelerate the internal wear and may cause failure. I like to be sure the fluid is of the right viscosity, without discoloration or presence of particulates that would show it is contaminated. If there is any doubt, one has to drain, flush the system, and then refill it to keep it operating at its best. And of course, always replace filters as per the manufacturer’s instructions to avoid harmful debris getting through the system.
Lastly, the pump should be tested to verify its operation in actual performance conditions. Keep an eye on system pressures, cycle speeds, and temperature stabilities; any unusual vibration or irregularity means underlying mechanical or operational issues need looking at. Keeping inspection records up to date after every check is also very important, as this allows trend analysis and hence the proactive resolution of recurring problems. By following this elaborate inspection procedure, a hydraulic dump pump will remain dependable and safely operative for a long time, thereby cutting down on downtime and maintenance expenditures.
Fluid Maintenance and Replacement
Correct fluid maintenance forms the foundation on which the hydraulic dump pump performs to the highest potential. Hydraulic fluid is the very essence of the system; it transmits power, lubricates, cools, and carries away contamination. With time, if left unchecked, the fluid may develop into a cause of inefficiencies or complete failure of the system.
Since the hydraulic fluid checks depend on equipment usage and manufacturers’ instructions, the practiced rule is once every two weeks while under normal operational conditions. The operator must always observe dark discoloration, unusual viscosity, or particulates in the fluid. Contamination from the ingress of outside matter, internal wear, and component degradation may, over time, seriously reduce the efficiency of the pump.
Fluid change intervals rely on operating load, environmental conditions, and fluid specifications, usually every year or every 1,000 operating hours in the absence of manufacturers’ instructions. The system should always undergo rigorous flushing during fluid change so as to remove all contaminants and avoid cross-contamination with the new fluid. Using high-quality hydraulic fluids recommended by the manufacturers will ensure compatibility with system seals and components while also increasing the overall life span of the equipment.
Closely following fluid maintenance schedules reduces the possibilities of cavitation, overheating, and premature wear, ensuring high dependability and efficiency of hydraulic dump systems through extended working hours.
Identifying Common Problems
Hydraulic systems, including dump systems, are prone to various operational problems when neglected in terms of maintenance or regular inspection. One of the most prevalent problems is contamination: dirt, debris, or water enters the hydraulic fluid, resulting in impaired system performance and even component wear. Contamination, if left unattended, can cause slow operations, diminished performance, or, in extreme cases, total system failure.
Another commonly occurring problem is the presence of air bubbles in the hydraulic fluid, which is referred to as aeration in the industry. These bubbles give the fluid spongy reactions, whereas with the presence of aerodynamic spurts, the system motions become very erratic; it also causes cavitation to become more probable. Yet ironically, leaks in hydraulic lines create a pressure drop, essentially draining far too much from the system’s efficiency and setting it up for overheating.
Seal degradation is another great plague, usually induced by time following temperature extremes, or the use of incompatible fluids. With worn seals, internal leakage hampers system pressure and eventually diminishes the performance of equipment. A good set of eyes should be kept out for early symptoms, such as unusual noises, slow cycle times, or visible leaks. A prompt identification and resolution of these issues do wonders for the functionality and lifespan of hydraulic systems.
Common Issues with Hydraulic Pumps in Dump Trucks
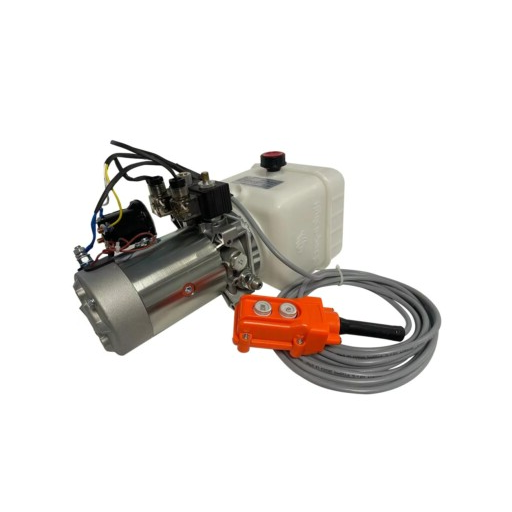
Leakage Problems
Leakage in hydraulic pumps for dump trucks is a common operational issue and can be classified into two main categories: internal and external leakages. Internal leakage occurs inside the pump housing due to wear and tear of internal components like the seals, gaskets, or pistons, thereby decreasing the fluid pressure and lowering system efficiency. External leakage happens when there are broken or poorly tightened joints, cracks in the pump casing, or worn-out seals that cause visible loss of fluids.
Technical data shows that hydraulic systems undergoing continuous leakage would face efficiency losses of up to 20 percent, thus directly influencing the performance of dump trucks and hiking the cost of operations. It is, therefore, critical to regularly inspect and maintain hydraulic systems so that any minor leak may be detected before it escalates into a major failure. Modern high-tech diagnostic tools, such as ultrasonic leak detectors and fluid flow sensors, can greatly aid in accurately locating the source of leakage. In addition, the use of superior hydraulic fluid together with components that can withstand extremes of temperature and pressure should be considered more so in order to avert the possibility of leaks developing as time rolls by.
Tackling these problems through preventive maintenance means more reliable equipment, less downtime, and longer heavy-duty hydraulic system life.
Overheating Issues
Overheating in the hydraulics realm is a common and quite destructive problem, where inefficient heat dissipation or losses of energy in the system are usually at the root of it. Should a hydraulic system operate beyond the optimum temperature range, accelerated degradation of the hydraulic fluid takes place, reducing its viscosity and the lubricating properties on the surface of the pump and valve. Hence, the reagent factor of wear on components seriously resultant damage to pumps, valves, and seals, thereby decreasing the efficiency and, at some time, outrightly disabling the system.
His pay, the cooling works well against overheating in the hydraulic system. Heat exchangers may be fitted to conduct the outward heat energy away quickly, or cooling systems may be set in place. Real-time data of the fluid temperature can be collected using sensors and telemetry so that preventive measures are taken before a predetention threshold is crossed.
Regular maintenance is equally important: unclogging filters and checking for blockages that restrict fluid flow are all crucial measures to control heat. Using the best kind of hydraulic fluids with high thermal stability will be favorable for the system when it is operating at high temperatures. By taking care of these issues, you can reduce expensive downtime and enhance the life of the hydraulic system so that it will perform well under severe conditions.
Performance Degradation
There are various reasons for performance degradation in hydraulic systems-contamination, wear, fluid breakdown, and improper system calibration. Consider contaminants that block fluid pathways—they can be dust, dirt, fine metallic particles, or even disintegrated material from rubber seals. Damage to precision components or increased friction is what eventually leads to reduced efficiency. Additionally, the wearing down of some major components, including pumps, valves, and actuators, limits their capacity to uphold the ideal pressure and fluid flow rates in the system.
In a way, fluid breakdown is influenced by high temperatures, oxidation, or the long operation of the fluid. This decreases the fluid’s lubricating ability and thereby increases the operation of cavitation and sludge formation. Apart from that, improper setting of system pressures will cause inconsistent operation, lower load-holding capacity, and lead to premature failure of components. Studies reveal that contamination and maintenance practices account for 80% of hydraulic system failures; thus, this explains the importance of frequent system checks and fluid analyses.
Proactive maintenance strategies like installation of an advanced filtration system and routine fluid sampling create a window for detecting malfunctions early. Implementing them would avoid the problems of performance degradation while enhancing operational efficiency and the overall reliability of the system.
Frequently Asked Questions (FAQ)
Q: What is a hydraulic pump for a dump truck?
A: A hydraulic pump for a dump truck is a crucial component that transfers hydraulic fluid to the hydraulic cylinders, enabling the dumping mechanism to lift and lower the dump bed. This pump is essential for the efficient operation of dump trucks, particularly in construction and heavy-duty applications.
Q: How does a PTO function in a hydraulic pump for a dump truck?
A: The PTO, or power take-off, is a device that connects the hydraulic pump to the truck’s engine, allowing it to draw power to operate the hydraulic system. When engaged, the PTO provides a means to power the hydraulic pump, ensuring that the dump truck can raise and lower its bed effectively.
Q: What types of hydraulic pumps are available for dump trucks?
A: There are several types of hydraulic pumps available for dump trucks, including gear pumps, vane pumps, and piston pumps. Each type has its advantages, and the choice depends on factors such as the required flow rate, pressure, and the specific application of the dump truck.
Q: What is the role of the hydraulic cylinder in a dump truck?
A: The hydraulic cylinder plays a vital role in a dump truck’s operation by converting hydraulic pressure from the pump into mechanical force. It is responsible for lifting the dump bed, allowing for the unloading of materials. The size and capacity of the cylinder determine how much weight the dump truck can handle.
Q: How can I select the right hydraulic pump for my dump truck?
A: To select the right hydraulic pump for your dump truck, consider factors such as the dump truck’s specifications, the intended use, the required flow rate, and pressure settings. It’s also essential to choose a pump compatible with your truck’s hydraulic system and ensure it meets all performance requirements.
Q: What is a relief setting in a hydraulic pump for a dump truck?
A: A relief setting is a safety feature in a hydraulic pump that prevents excessive pressure buildup in the hydraulic system. If the pressure exceeds a certain threshold, the relief valve opens, allowing fluid to escape, thereby protecting the hydraulic components from damage and ensuring safe operation.
Q: Can I find remote-controlled options for hydraulic pumps for dump trucks?
A: Yes, there are remote-controlled options available for hydraulic pumps for dump trucks. These systems allow operators to control the lifting and lowering of the dump bed from a distance, improving safety and convenience during unloading operations.
Q: Where can I shop for hydraulic pumps for dump trucks?
A: You can shop for hydraulic pumps for dump trucks at various automotive supply stores, specialized hydraulic equipment retailers, and online marketplaces. Ensure that you choose reputable suppliers that offer quality products and provide necessary information about compatibility and specifications.
Q: What are the common parts of a dump truck hydraulic system?
A: Common parts of a dump truck hydraulic system include the hydraulic pump, hydraulic cylinders, hydraulic fluid reservoir, hoses, valves, and filters. Each part works together to ensure the system operates smoothly, enabling the dump truck to perform its intended tasks effectively.